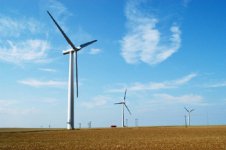
حدود 200 سال پیش از میلاد مسیح، نخستین آسیاب بادی توسط ایرانیان ساخته شد و سپس در قرن های دوازدهم و سیزدهم میلادی، اندیشۀ به كارگیری انرژی باد در آسیاب و یا پمپ بادی از ایران به آمریكا و اروپا منتقل شد. ولی باتوجه به وجود منابع گستردۀ انرژی های فسیلی و نفت، كاربرد این انرژی به روشی غیركارآمد و غیرقابل قبول از دیدگاه فاكتورهای اقتصادی تبدیل شد. تا این كه پس از سال 1973 با توجه به بحران انرژی، اندیشۀ پیشرفت و به كارگیری انرژی های بازیافت پذیر به عنوان جایگزین مناسبی برای منابع محدود سوخت های فسیلی و تنها راه از بین بردن مشكلات ناشی از مصرف سوخت های فسیلی برای محیط برای محیط زیست، منجر به رویكرد دوبارۀ بشر به كاربرد انرژی های بازیافت پذیر و به ویژه انرژی باد شد. امروزه نه تنها از انرژی باد برای استخراج آب استفاده می شود، بلكه با ظهور توربین های بادی نوین و گسترش نیروگاه های بادی در قالب احداث مزرعه های بادی، به كارگیری این انرژی برای تامین الكتریسیته لازم نیز مدنظر قرار گرفته است؛ به گونه ای كه بنابر آمار به دست آمده تا پایان سال 2002، معادل 30166 مگاوات برق نیروگاه بادی در سراسر دنیا نصب شده است.
اگر به میزان نیروگاه های بادی نصب شده در دنیا از سال 1996 تا 2001 توجه كنیم، متوجه می شویم كه آهنگ رشد این صنعت در این پنج سال، 5/39 درصد بوده است؛ به گونه ای كه كشورهای پیشرفته ای چون آلمان و دانماركبه ترتیب تولید 5/12 و 29 درصد برق كل كشور خود را با به كارگیری انرژی باد تا سال 2010 میلادی، سرلوحۀ برنامه پیشرفت خود قرار داده اند. مواردی چون تولید برق بدون آلوده سازی محیط زیست، قابلیت نصب و راه اندازی سریع، هزینه تعمیرات و نگهداری كم و به كارگیری انرژی خدادای باد، همه از ویژگیهای یگانۀ نیروگاه های بادی هستند. اما در كنار این برتری ها، عیب بزرگ این صنعت- كه دائمی نبودن باد است- نمایان می شود.
پره، به عنوان مهم ترین جزء توربین بادی، وظیفۀ گرفتن انرژی جنبشی باد و تبدیل آن به حركت دورانی به منظور به حركت درآوردن گیربكس و ژنراتور را برای تولید برق به عهده دارد. پره های توربین بادی نوین امروزی براساس اصول پیشرفتۀ آیرودینامیك ساخته می شوند و برخلاف توربین های قدیمی كه با افزایش سطح مقاوم در برابر باد به حركت در می آمدند، به واسطۀ فرار باد و افزایش نیروی برآ به حركت واداشته می شوند.
امروزه با توجه به رشد و پیشرفت شیوه های ساخت و گسترش مواد اولیه، به كارگیری فناوری كامپوزیت ها برای غلبه بر مشكلاتی همچون وزن و فرآیند ساخت، در سرلوحۀ دید صاحبان صنایع گوناگون قرار گرفته است است. پره های توربین باد نیز باتوجه به طول بسیار بلند و حجم عظیم بارهای وارده، نیازمند استحكام بسیار مناسب، برای مقاومت در برابر بارهای گوناگونی هستند كه بر آنها وارد می شود. همچنین از سوی دیگر، باید وزن آنها تا حدامكان كاهش یابد و این، تنها با به كارگیری فناوری كامپوزیت ها ممكن است؛ به گونه ای كه باتوجه به معماری قابل تغییر این مواد، میتوان آنها را در جهت موردنظر تقویت كرد تا از اضافه وزن بیش از حد سازه جلوگیری شود و همچنین خواستگاه هایی چون خیز انتهایی و مقاومت در برابر ارتعاشات آزاد نیز در بازۀ بهینه باشند. از سوی دیگر، افزون بر ویژگیهای ممتاز عمومی بیان شده، یكی دیگر از ویژگیهای یگانۀ این مواد كه آنها را در رأس مواد دیگر قرار می دهد، مقاومت بسیار مناسب آنها در برابر بارگذاری چرخه ای یا همان پدیده خستگی است پره های توربین باد نیز به علت ویزگی دگرگون باد، در برابر این پدیده قرار دارند و از آنجایی كه طول عمر و هزینه های تعمیر و نگهداری- از دیدگاه صرفۀ اقتصادی- از موارد خطیر در طراحی سازۀ آنهاست، به كارگیری مواد مركب تنها راه حل چیره شدن بر این مشكل است.
هم اكنون كارخانۀ سدید صبا نیرو در ایران، پره های توربین باد 660 كیلو وات را تولید می كند. این پره ها كه طولی در حدود 23 متر دارند، تمام كامپوزیت هستند و تنها در بخش اتصال به ریشه آنها یك رینگ آلومینیومی به كار رفته است كه از درون و بیرون با لایه های كامپوزیتی پوشانده شده است. این پره ها از دو بخش اساسی پوسته و شاه تیر (Spar) تشكیل شده است.
پوسته كه بخش خارجی پره است، از دو بخش پوسته بالایی و پایینی تشكیل شده است و وظیفۀ تامین پروفیل آیرودینامیكی جریان را به عهده دارد. پوسته به خاطر ملاحظات سازه ای و آیرودینامیكی، از ریشه به نوك، باریك می شود و برای حفظ زاویۀ بهینه حمله، در سراسر طول خود دارای پیچشی برابر با 15 درجه است. این پوسته از نوك تا فاصله 5/4 متر از ریشه، دارای مقطع های بالواره ای شكل است كه بزرگترین طول وتر بالواره در این مقطع، نزدیك به 2 متر است. بالواره های به كار رفته در پره، از نوع ویژه ای هستند كه شكل نخستین آنها از بالواره های بال هواپیما الهام گرفته است. در ساخت این پوسته یك قالب كامپوزیتی پیوسته به كار می رود كه دارای دو تكۀ بالایی و پایینی است.
در انتهای این قالب، یك سیستم كنترل مجهز قرار دارد كه بنا بر برنامۀ از پیش تعیین شده در مراحل گوناگون، فرایند مكش و پخت را بنا بر چرخۀ هر مرحله بر محصول حاكم می كند. در نخستین مرحله، تمام سطح های قالب بالایی و پایینی با یك ماشین ویژه و با رولرهای دستی به پوشش ژلی سفیدرنگ آغشته می شوند. سپس قالب بسته شده و پوشش اعمال شده پخت می شود. در مرحلۀ بعدی لایه های بریده شده با دستگاه برش براساس الگوی از پیش تعیین شده در محل های ویژۀ خود قرار می گیرند. برای سرعت بخشیدن به كار، وزن كمتر و كیفیت بهتر محصول نهایی، در ساخت این پره ها مواد كامپوزیتی پیش آغشته (الیاف شیشه به همراه رزین اپوكسی) به كار می رود. به هنگام لایه گذاری نیز، بخشهای ویژه ای به فوم پی وی سی مجهز می شوند. پس از پایان لایه چینی نوبت اعمال مواد مصرفی مربوط به فرایند مكش و پخت است. سپس قالب بسته شده، پس از اعمال مكش در فشار ویزه در دمای 100 تا 120 درجه سانتیگراد پخت انجام میشود. پس از پایان این مرحله، پوسته آماده شده است. بافت الیاف پیش آغشته به كار رونده در پوستۀ پره از دو نوع كلی الیاف دو سویه و سه سویه است كه به ترتیب الیاف با جهت 45-/45+ درجه و 45/0 9/0 درجه را در بر می گیرند.
شاه تیر كه خود از دو بخش تیر اصلی و تیر فرعی تشكیل شده است، بخش اصلی سازۀ پره را تشكیل می دهد كه در درون پوسته قرار گرفته و وظیفۀ آن ایجاد سفتی و استحكام مناسب برای رویارویی با بارهای اعمالی به هنگام كاركرد پره است. تیر اصلی كه دارای مقطع مستطیل شكل است براساس قرار دادن لایه های گوناگون و فوم PMI بر روی یك مندرل فلزی با طولی در حدود 31 متر تولید می شود . پس از پایان لایه چینی و اعمال مواد مصرفی لازم برای فرآیند مكش و پخت، با یك روكش سراسری كه مجهز به المان های گرم كننده است، پوشانده میشود و به وسیلۀ سیستم كنترلی رایانه ای و نمودار مشخصی در دمای بین 98 تا 105 درجه سانتی گراد پخت می شود. تیر فرعی نیز با فرآیند مشابهی بر روی یك مندرل كوچك تر تولید شده (برای ایجاد یك تیر پیوسته به طول 23 متر) در انتها به نوك تیر اصلی متصل می شود. در تولید تیر نیز الیاف پیش آغشته با بافت كلی تك سویه و دوسویه به كار می روند كه الیاف تك سویه برای رویارویی با گشتاورهای خمشی و نیروهای كششی در جان تیر نهاده میشوند و الیاف دوسویه 45-/45+ درجه برای رویارویی با برش در بال تیر قرار می گیرند.
در آخرین مرحله از تولید پره كه به مرحلۀ مونتاژ معروف است، تیر باید در درون پوسته نهاد شود. بدین منظور، بخش های نشیمن گاه تیر بر روی پوسته زیرین و سطح بالایی تیر كه به پوسته بالایی وصل خواهد شد، با ماشین چسب كاری به چسب آغشته می شوند و سپس تیر در درون همان قالب تولید پوسته بر روی پوستۀ زیرین نهاده شده، قالب پره بسته می شود. برای آخرین بار، فرآیند مكش و پخت صورت می گیرد و در پایان پره به صورت یك مجموعه از قالب خارج می شود.
لازم به ذكر است كه در فرآیند تولید، پره به سیستم محافظت در برابر رعد و برق مجهز میشود. این سیستم، متشكل از یك طناب بلند است كه از نوك پره تا رینگ آلومینیومی ادامه می یابد.
پس از پایان فرآیند تولید، پره های تولیدی به سالن عملیات نهایی منتقل می شوند. در این سالن، سطح پره ها كاملاً پرداخت شده و تمام سطح ها با ابزارهای كنترلی ویژه، برای اطمینان از شكل هندسی مناسب بازبینی می شوند. تعمیرات موردی نیز بر روی پره در این بخش انجام می شود. در این سالن، برخی از كارها از پیش تعریف شده بوده و برخی دیگر با توجه به محصول تولید شده تعریف می شوند. در آخرین مرحله در سالن عملیات نهایی، قطعه ای به نام یاتاقان به محل اتصال ریشه وصل شده، پره ها بالانس شده و پس از كشیدن روكش محافظ ویژه، برای انتقال به سایت به بخش انبارش منتقل می شوند. وزن پرۀ تولید شده بدون در نظر گرفتن بخش های فلزی لازم برای اتصال به توربین 1150 كیلوگرم است. این پره براساس یك دوره كاركرد 20 ساله طراحی شده است. تمام فرآیند تولید به وسیلۀ متخصصان كنترل كیفیت، بازرسی شده و در شناسنامۀ پره ثبت می شود كه این كنترل، تمام فرآیندها را- از آزمایش مواد اولیه در آزمایشگاه گرفته تا شیوۀ لایه چینی، پخت، وزن كردن نهایی پره و گزینش سه پره برای یك روتور- شامل می شود.